By John Hunter, author of the Curious Cat Management Improvement Blog (since 2004).
One of the items Toyota highlights on their web site is winning the Deming Prize in 1965.
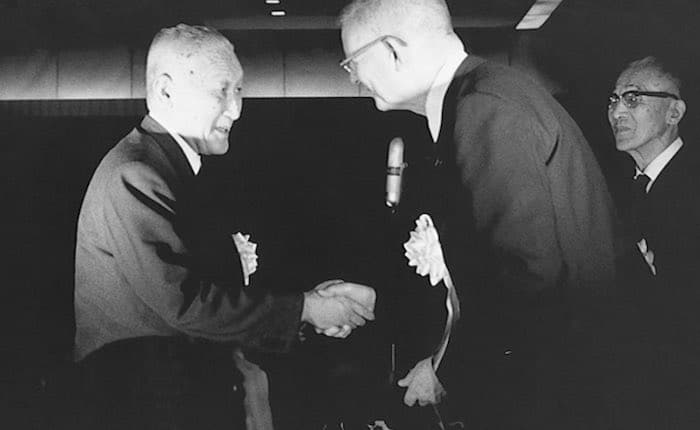
From the Toyota website:
Receiving the Deming Application Prize strengthened Toyota Motor Co., Ltd.’s resolve to push ahead with further TQC initiatives, and based on the points cited by the Deming Prize judges the company set the following policies:
- To promote all-around quality control, including at affiliated companies such as suppliers and dealerships.
- To establish simple and effective management systems without being preoccupied by form, paying particular attention to ensuring checks and actions, and rotating the management cycle rapidly.
- To enhance overall planning and, from a long-term perspective, achieve swift and precise decision making and execution through coordination among management structures.
Under this policy, in February 1966 an eight-company QC Liaison Committee was established among Toyota-related companies, creating a framework for deliberating specific measures to involve all Toyota-related entities in quality assurance actions.
Toyota continued their efforts and became the first company awarded the Japan Quality Medal in 1970 (a company is eligible 5 years after winning the Deming Prize).
From Toyota’s Japan Quality Medal page, 1970 Basic Toyota Corporate Policy:
- Harness resources in and outside the company to grow and become a Global Toyota
- Practice ‘Good Thinking, Good Products’ at all times to raise the reputation of Toyota as a maker of quality products
- Establish mass production systems, achieve low prices, and contribute to the growth of the Japanese economy
- Be aware of the public nature of the automotive industry and contribute to the welfare of society
Note: Items 1 through 3 were formulated in fiscal 1963 (ended June 1964). Item 4 was added in fiscal 1970 (ended June 1971).
The Toyota history website includes a view into Toyota’s learning and continual improvement of their management system. In 1979:
A two-year management capability improvement program was implemented with the department and section managers specifying topics for operational improvement. Compared to the improvements being made at manufacturing sites, increases in the efficiency of management and administrative departments was lagging and the number of managers who had not experienced the Deming Prize screening was increasing, resulting in a rising sense of a need for improvement of the management skills of department and section managers.
Toyota understood the importance of adopting these ideas throughout the organization back in the 1970s. And some people still today think of these ideas as limited to manufacturing operations. There is still such a long way to go in improving the practice of management.
Meanwhile [1983], along with the establishment of the TQC Promotion Department President Shoichiro Toyoda announced a policy for the management team to take the lead in tackling quality control. Accordingly, the 1st QC Study Group, attended by all board members, was held over three days and two nights in June 1983. The themes for discussion, which included “integration and increased efficiency in sales, product planning, development, and production” and “strengthening of dealer corporate systems”, focused on internal coordination and coordination with dealer, as that was important immediately after the merger. From that year on, the QC training seminar for executives meeting came to be held every year, and in 1991, its ninth year, the group was renamed the Executive Study Group.
Toyota’s long term commitment to continual improvement of management practices has lead to an excellent management system. That management system is often referred to as the Toyota Production System and was also given the name “lean manufacturing.” Over time the lean manufacturing name has morphed as it is used by many people but at the core it is the Toyota Production System.
Shoichiro Toyoda, Honorary Chairman and director of Toyota, in 1980:
Toyota Motor Kyushu (Japan) received a Deming Prize in 2016, the first Deming Prize for Toyota this century.
Related: The Birth of Lean (book) – Deming and Lean: The Disparities and Similarities – Podcast Discussing Dr. Deming’s Ideas, The Deming Institute and Toyota – The 2 Pillars of the Toyota Way: Continuous Improvement and Respect for People – Interview with Masaaki Imai