By John Hunter, author of the Curious Cat Management Improvement Blog.
Fred Warmbier, CEO of Finishing Technology and Kelly Allan, Senior Associate of Kelly Allan Associates and Chair of the Deming Institute Advisory Board are guests on the latest Deming Institute podcast.
Fred and Kelly discuss the Deming journey of Finishing Technology, which they also have been documenting in their excellent New York Times small business blog. Fred first discovered Deming’s management ideas in September 2013 when he attended a Deming Institute 2.5 day seminar presented in partnership with Aileron (a non-profit with a mission of “unleashing the potential of private businesses through professional management”).
We try to develop our critical thinking skills as a team and we asked people what is your theory of this?
And that thinking is taking hold, as Fred continued, recently there was an issue with the results of a process and when questioned the employee said “I’ll test my theory and get back to you.” Great words to hear.
We need to operate in a completely different way so we can be more effective and more efficient in the future.
Fred talked about the challenges for a leader trying to change from a short term focus of getting the work out the door and thinking of the organization as a system and how to improve. The transition is a challenge. The rewards of improving are that less energy is needed to deal with so many short term challenges. Fred sees that starting to happen:
As we are moving more toward the Deming management methods it is becoming calmer; we will have less stress in our environment.
He admits he isn’t sure that is obvious to everyone at work yet. This is often the case. Changes often cause some people to worry. A few people are lucky to get big initial gains directly in their area. And a few can see how the organization as a system is improving significantly. But it often takes quite a bit of improvement before nearly everyone agrees these new management practices really are making a big difference. There is often a fairly wide variation in people’s perceptions even for a few years of making improvements.
We are really only 6 or 7 or 8 months into it [the transformation to Deming management methods].
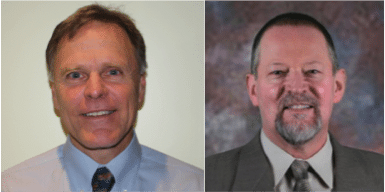
If you read the New York Times blog (and if you are not, you should) it is amazing how they are adopting the thinking so quickly. Fred really shows that he is thinking differently, which I find is often lacking. Often organization take a few new tools and a few concepts that they apply in isolated projects. But really thinking differently and deeply often doesn’t happen for years (outside of a couple people in each organization that dive in deeply and understand the implications and potential). Fred gives a lot of credit to Kelly and I agree that having a knowledgable consultant makes a huge difference in how effectively an organization can improve.
He also discusses standardized work instructions (process sheets) and one of the things I think really can make a big performance difference. He discusses how so many of the process sheets don’t actually correspond to the actual process. Workers know the supposed process won’t work as well so they take other action but that creates all sorts of problems and risks. But when you are focused on getting the work out the door not on long term reliability that is what happens.
Kelly Allan:
Changing the system in which people work changes the culture… [don’t try] to change the behaviors of people [directly], change the rules and policies of the system [and behaviors will change].
Related: A Blog Following the Management of Finishing Technology Using Deming’s Ideas – Bob Browne Discusses His Experience Applying Deming’s Ideas as a CEO of the Great Plains Coca Cola Bottling Company – Support of Top Management is Not Sufficient – 94% Belongs to the System