Guest post by Michael Ballé (repost from his Gemba Coach column on Lean.org)
Dear Gemba Coach,
For product development you need creative (maybe even chaotic) people. Are those people suited to follow such a structured method as lean? Like trying to achieve one-piece-flow in product development?
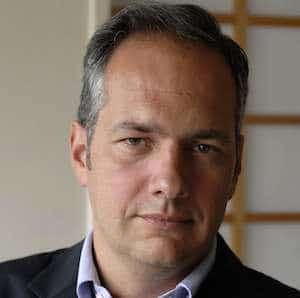
Thank you. What an interesting question! As a writer and novelist, I like the idea that it’s okay to be chaotic! But aren’t we making assumptions about the nature of creativity? Let’s take a gemba example of a product we all have experience with: a gasoline pump. In product development terms, this product evolves at several levels:
- Solving quality problems of products now in production through engineering patches (or adding customer-required options)
- Introducing regular product refreshes through engineering improvements to keep the customers (gas stations) interested in refurbishing
- Reducing work content through smart engineering in order to drive manufacturing costs down
- Making step change improvement to key functionalities such as the meter and the pump to keep market leadership
- Making technological breakthroughs to invent the dispenser of the future, with technologies such as connectivity, VGA screens, Big Data diagnostics and so on.
Tom Edison and Steve Jobs
Each of these specific change points have their own rhythm, or takt, and require very different types of engineering and, in particular, different types of creativity:
- Quality problem solving creativity is centered on solving narrow, detailed problems as locally as possible without impacting the rest of the design. Doing so successfully demands full mastery of existing standards and a good dose of cleverness.
- Product refreshes are based on changing specific product features, and again, require a full understanding of standards. A successful product refresh is one where as little as possible is changed to the full design, certainly no change of the product architecture, but specific features can be visibly improved for customers. The creativity required there is one based on full experience and mastery of standards with very local experimentation to minimize changes: every design change has a probability of failure and a number of points of impact. We need to be very cautious and frugal about these changes.
- Reducing work content is mainly about modularity within the existing product architecture, and a lot of the creativity there involves teamwork with suppliers in terms of which parts come as separate components and which can be standardized as a full sub-assembly.
- Step changes in key functionality should be made within existing interface standards, and necessitate to delve deeply into the science of the function. For instance, coming up with a new meter for the dispenser meant revisiting everything the guys knew about hydraulics, fluid dynamics and mater/fuel chemical interactions. This definitely requires another type of creativity, which is that of the dodged scientist who will, in Edison’s terms, not fail because she succeeded at the 1000th attempt, but learned 999 ways that won’t work.
- Technology leaps require yet again another sort of creativity, and someone in the team had better have a Steve Jobs type of person, because it’s first and foremost about a total product vision and then knowing how to work with engineers to come up with a product reality that fits that vision – this is fashion designer type of creativity, and indeed, you might say, artistic and perhaps chaotic, but in any case rather a rare occurrence.
Putting the leap aside, which most companies I know are not that well set-up to achieve (fortunately, few companies have Steve Jobs as a direct competitor), the bulk of product development is not about total product reinvention but about making smart changes that have controlled impact on the full design. The secret to products that work (and that customers buy) is being both conservative on standards and daring on a few, visible features.
Overburdened Engineers
As a result of aggressive financial management, most companies I know are currently underinvested in engineering –- an easy budget to cut as the output is not immediately visible unless one calculates a clear takt of engineering changes. As a result, engineers tend to be overwhelmed by work covering at least the four previous types of engineering demands. After seven (plus two, minus two) work items on someone’s mental work desk, psychology tells us any human is saturated and starts shifting mindlessly from one pressing issue to the next without time for deeper thinking and self-reflection.
Peace of mind and time to think are absolute requirements for creativity and intuition. Chaos, a necessary ingredient of serendipity, only works for people obsessed with a clear question and with the mental space and disposition to keep working on it over time. If you’ve been mulling over something for long enough, then, yes, a brilliant idea will come in the shower or poking your fork in egg yolk at breakfast, or going to an art gallery – only because your mind is running the same questions on and on in its back office. The front desk is free enough from distractions that the little guy in the mind can browse files and make unexpected leaps of intuition. If the front desk is busy all day long, this is unlikely to ever happen.
In these terms, one-piece-flow projects create the best conditions for true creativity. Without a serene, one-by-one, and yes, structured approach, engineers are overburdened with too many demands on their time and have to juggle too many different burning fires, which is chaos, certainly, but not of the creative kind. The peace of mind of obsessing on one topic at a time is a general framework that liberates engineers to create some real creative chaos by thinking deeply into the issue and welcoming serendipitous insights.
Michael Ballé recently co-authored (with Freddy Ballé) – Lead With Respect: A Novel of Lean Practice.
End of guest post
I (John Hunter) think Michael Ballé’s response does a great job of explaining why a good management system aids the creative process. This idea that a management system (Deming based, lean thinking etc.) results in an inflexible structure that inhibits creativity and innovation is completely wrong. Though I do understand that the way many management systems operate (even some calling themselves Deming based or lean thinking) do create those conditions. But that is a misapplication of the ideas not an end result due to the management system requirements.
Related: Standard Work Instructions are Continually Improved; They are not a Barrier to Improvement – Managing Innovation – People are Part of the Management System